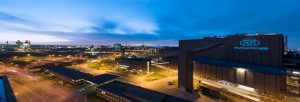
ThyssenKrupp: Document Automation with DocBridge® solution
Excerpt: In 2015, when thyssenkrupp Steel Europe AG brought output management back in-house, it represented a basic structural change. Instead of a traditional print shop, a company-wide Competence Center for Print and Digital Media was created, laying the foundation for multi-channel document processing.
About the author: Carsten Lüdtge, a qualified journalist (University Degree: Diploma) and specialist editor, is responsible for press and public relations at Compart, an international manufacturer of software for customer communication, and is … Read more
Contents
In the mid 2010s, the board of thyssenkrupp Steel Europe (tk SE) instructed the corporate divisions to scrutinize all outsourced services and, if possible, bring them back in-house. That included document production, which until then was being handled by an external service provider. The reason was the company’s worldwide cost-cutting program prompted by the then steel crisis.
After insourcing and the associated consolidation into a single in-house service provider, additional services were added (scanning, enveloping, franking, mailing, etc.) to create a “Competence Center for Digital and Print Media” with locations in Duisburg, Bochum and Dortmund. The center has 65 permanent employees and 25 probationary employees, who are being trialed in various work areas after an extended illness. Most of the latter have physical or mental limitations.
“In our company, inclusion is not just a word, it is an engrained daily practice,” says Oliver Helfrich. The head of the competence center emphasizes that integrating persons with disabilities requires sensitivity. “The art lies in finding a reasonable compromise between productivity and strain on the employee.” Therefore, employer and employee carefully explore possible fields of activity. “Every case must be decided individually, limits sounded out. How far do the cognitive and physical abilities of the person extend? Is he up to the stress and the daily routine? What are his needs?”
Together with the employee, a specially trained team of physicians and psychologists develop a suitable employment model. And that’s not all. At thyssenkrupp Steel Europe AG, inclusion also means reintegrating employees whose careers were derailed for various reasons (e.g., serious illness, accident, family problems) and are now looking to get back on track.
High degree of automation guarantees production reliability
Oliver Helfrich and his team therefore face a serious challenge. For one thing, new expertise must be developed and existing knowledge redirected. For another, the workflows need to be structured such that even the employees with a handicap can be integrated into the production process. Partnering together with Canon, Oliver Helfrich and his colleagues developed a concept for the gradual establishment of a company-wide competence center.
Their goal was to network with other company divisions, thereby acquiring more and more orders. Oliver Helfrich: “From a global standpoint, we also wanted to better coordinate co-existent capacities at the different locations and to automate the printing process even more, using an appropriate IT solution.”
But the question remained: which IT solution? “We had absolutely no experience in choosing suitable software,” recalls Helfrich. “The only thing that was clear was that the solution had to cover all the facets of our document processing operation.” Their search came to an end in 2013 at the Compart booth at the DMS Expo in Stuttgart, where they first encountered DocBridge Pilot. Helfrich remembers that they were immediately impressed with its ease of use and broad functional scope.
It is primarily the high degree of automation that ensures high reliability in document production, according to the competence center head. The workflows are clearly structured and are controlled by the system. “The risk of job mix-ups, misprints, and incorrect mailings drops to zero with DocBridge Pilot,” he sums up.
Custom launch: printing and mailing of invoices from ERP
The company began by converting production of invoices and delivery notes, specifically because the process is not very complicated and is also highly profitable. Handling these jobs is relatively uncomplicated for the competence center, which has its own enveloping and franking production line. The transition proceeded without major problems, on time and on budget.
Previously, these documents and their control files were retrieved from various ERP (Enterprise Resource Planning) systems, stored on an FTP (File Transfer Protocol) server, and then downloaded and processed by the external service provider.
Soon the mobile communications bills of all company employees will run through the new system. Specifically, DocBridge Pilot splits the monthly consolidated bill from the mobile phone provider into individual documents for each employee and bundles it, if needed, with other documents going to the same employee. thyssenkrupp Steel Europe AG hopes to further cut costs in this way by better utilizing bulk mail discounts. The company also has its eye on other internal processes that can follow suit.
Growing order volume and digital mailing
Furthermore, thyssenkrupp hopes to use digital delivery in future. In any case, Oliver Helfrich expects the ratio of physical and digital documents in the company to change. The board has expressly requested “digital delivery to the entire world.”
But paper still predominates. Today the company produces over a million documents every month, 70,000 of them invoices and delivery notes in Duisburg. As part of the restructuring, three new high-performance full-color digital printers were installed there, Dortmund and Bochum. The new overall solution follows the principle of flexible, modular standardization and the newly created interfaces for printing from the ERP systems can also be used for other scenarios in future, such as for applications in the personnel department or as a fixed component of a company-wide service offering in the form of a digital mailbox.
In any case, Oliver Helfrich and his team are equipped with the best, because the new system with DocBridge Pilot at its core can easily be expanded for new jobs. It is precisely this scalability and the openness of the interfaces of the software solutions used that guarantee high investment protection as well as a quick return on investment (ROI). At the same time, additional control software monitors process quality by seamlessly monitoring the cycle for each document right up until dispatch.
Postage costs drop by €60,000
For Oliver Helfrich, the benefits of restructuring are obvious: lower administrative costs, standardized data formats, and fewer interfaces. But above all, the significantly lower mailing costs speak volumes. The company saved more than €60,000 for invoices and delivery notes alone. DocBridge Pilot helped make it possible. The software is able to bundle documents from different sources into postage-optimized mailings. “Utilizing bulk mail discounts resulted in tremendous savings that guarantee the cost-effectiveness of our entire document processing operation,” summarizes Oliver Helfrich.
For him and his team, the restructuring is the dawn of a new age, and not only because document production was brought back in-house. It is really about a new self-concept: Phase out the simple in-house print shop (ever narrower margins and increasing competition in the traditional print business do not bode well in any case) and move toward a professional service provider for multi-channel output management. “Thanks to the cooperation with Compart, a proven specialist in multi-channel document processing, and Canon, we’re in a position both technologically and organizationally to fulfill every kind of order with high quality and on time.”
New services are now gradually being added to the portfolio. Recently, for instance, Oliver Helfrich and his competence center were certified by the Deutsche Post for IT franking. Other measures, including those aimed at digitalization, are being planned.